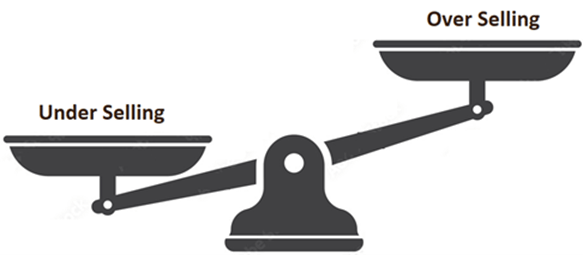
Underselling and overselling are common challenges for most retailers. On the one hand, companies strive to place just enough quantities of goods at the right locations, particularly at the right stores to enable buy-online-pickup-in store (BOPIS). On the other hand, companies fear the risk of stocking excess inventory, which needs to be at a deep markdown for selling. Having too much stock (overstocking) eats into margin while having too little stock (understocking) risks losing customers. So, how can retailers successfully utilize safety stock dynamically?
To prevent overselling, businesses set aside a part of their inventory called “safety stock.” Safety stock is the additional stock of an item held at a location to meet the future customer demand without resulting in stockout.” Typically, the safety stock is at a status value of either one or two units per SKU per location as a one-time activity. Safety stock is also used as a buffer stock to protect fill rates against fluctuating supply-demand. For example, if a retailer has 1,000 store locations across the nation, it blocks 1,000 to 2,000 units that are not available to sell online. This can result in the under-utilization of this parked inventory (underselling).
Impact of Safety Stock on Customers and Retailers
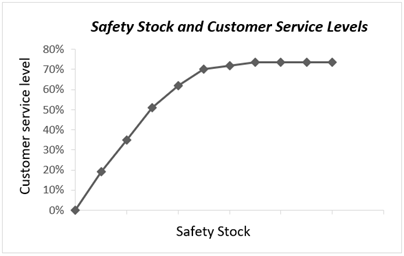
To ensure high customer service levels, retailers tend to err on the side of caution and have a few extra stocks for “just in case” scenarios. From the graph on the left, the higher the safety stock, the higher the service level. This approach to determining safety stock value may be simpler but not better.
Despite a high safety stock, brand retailers typically run into out-of-stock and backorder situations for products with less inventory depth. Brands usually maintain a safety stock of two to three units in each store. For products with an inventory depth of 10 units or less, retailers typically block 30-40% of inventory in each location, which is not available to sell. This creates lost sale opportunities. Finally, in a desperate attempt to sell leftover stocks, store managers often markdown product prices and sell them for clearance prices with less or no profit margin.
Static Vs. Dynamic Safety Stock
If demand for a product is stable, then maintaining static safety stock makes sense. Whereas if the demand for a product is dynamic, then maintaining static safety stock results in either stockouts or excess inventory. It’s critical to maintain dynamic safety stock for a product whose demand is fluid. In the retail sector, due to promotions, seasonality, and customer taste, the variable or dynamic trend of demand for a product is inherent.
Dynamic Safety Stock Critical for Dynamic/Variable Demand
The intelligent dynamic safety stock mechanism identifies whether a product needs safety stock at a location and, if so, how much. Dynamic safety stock uses machine learning (ML) and predictive algorithms to calculate the optimal value of safety stock at each location without any manual intervention. It considers numerous attributes such as demand spikes, supply disruptions, selling velocity, product price, promotions, seasonality, and location fill rate while calculating optimal safety stock value.
Dynamic safety stock isn’t a single value for a product. Dynamic safety stock is a set of values for the same product at the same location for each selling channel. It can provide the right amount of safety stock value for each selling channel based on past data. For example, the below graph represents sample safety stock value for different selling channels.
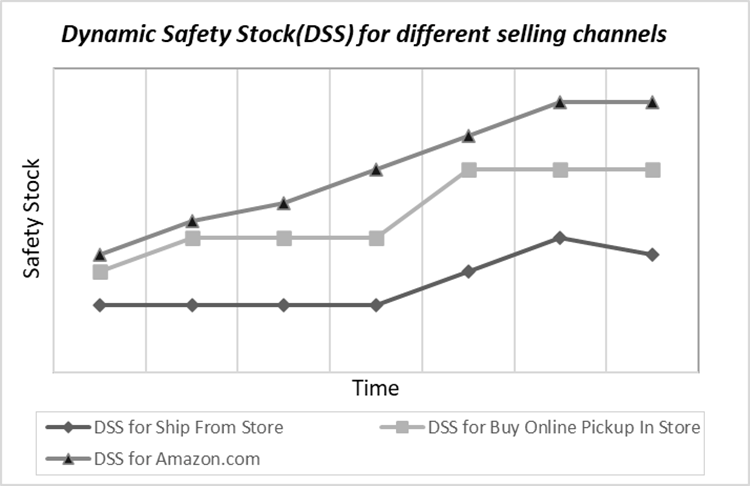
Update Safety Stock Dynamically
Calculating the safety stock is not a one-time activity and certainly does not follow a “one-size-fits-all” approach. Casting a wide safety net by having a safety stock of two or three units for all products is rudimentary and inefficient. Dynamic safety stock can unlock numerous benefits such as higher inventory utilization, increased revenue, and higher customer satisfaction. By analyzing your current stockout rates and lost sales due to stockouts, we will reveal the current performance of your safety stock.
ML and artificial intelligence (AI) powers Blue Yonder’s Dynamic Safety Stock capability, part of Luminate® Commerce’s Order Management microservices. It recommends a precise level of safety stock (only if needed) for each selling channel at the right time to delicately balance between excess inventory and higher customer service levels. This capability further maximizes the sale probability of safety stock based on ML capabilities. Suppose you’re ready to take the guesswork out of your current safety stock performance. In that case, the Blue Yonder team can help you unlock the value of dynamic safety stock for your organization without any manual intervention.