This blog post was co-authored by Anmol Khurana and Tommy See.
Since the Suez Canal disruption earlier this year, container and port capacity constraints have caused tremendous impacts to many supply chains around the world. Now all major ports in the United States are currently experiencing unprecedented congestion and labor shortages, leading to product stockouts and inflation — as well as significant supply chain challenges for retailers, manufacturers and logistics providers. While some critical U.S. ports have expanded their working hours, almost 200,000 shipping containers, with cargo worth more than USD 25 billion, remain on ships off the coast of Los Angeles as retailers scramble to ensure store shelves are stocked in time for the holiday season. In fact, some analysts now believe the worldwide supply chain crisis will persist until at least 2023.
The world’s largest and most powerful retailers are navigating their way around this crisis by chartering private ships and buying cargo planes. Similarly, big consumer product companies have the brand power and resources to explore costly strategies like shifting production, reformulating products and enlisting backup suppliers. How can companies that lack such massive resources continue to stay competitive in this environment? Unable to make reliable promises to retail customers or consumers, most enterprises are lost in a sea of uncertainty today, unable to predict when they will receive expected shipments — and watching helplessly as both customer loyalty and profit margins slowly erode. The recent announcement of escalating fines on containers that are past their dwell time, puts additional pressure on companies across the network. At the Port of Los Angeles and the Port of Long Beach alone, this impacts approximately 60,000 containers with cargo worth more than USD 2.6 Billions, both retailers and logistics providers would take a hit with reduced margins and higher operating costs.
«Upstream visibility is at its premium, where are your parts, where are your components if you are a manufacturer, for you to have finished goods routed down to your customers” says Girish Rishi, CEO, Blue Yonder, in a recent conversation with Fox Business. As with nearly every challenge, having visibility to disruptions and understanding the potential impact of such disruptions is critical for companies to ensure optimum service levels.
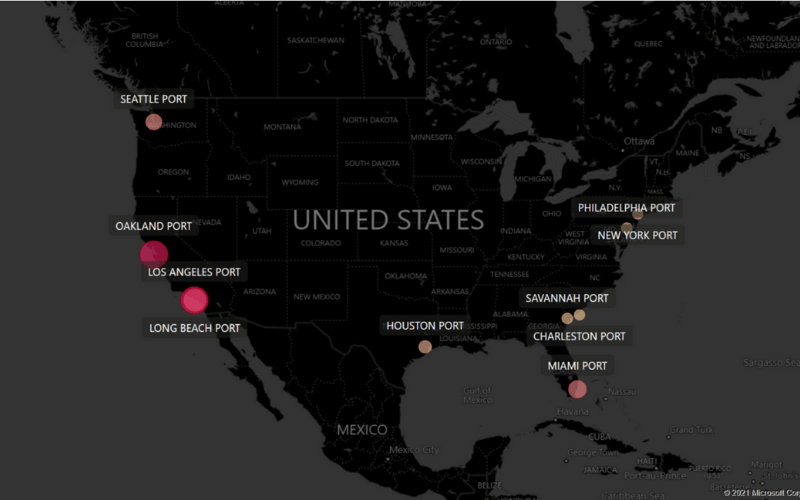
Blue Yonder’s Luminate Control Tower (LCT) software-as-a-service (SaaS) is purpose-built to deliver near real-time visibility across the complex, end-to-end supply chain. Luminate Control Tower acquires enterprise data from various source systems (customers, orders, inventory, shipment, etc.) and combines it with near real-time events (weather, maritime traffic, port conditions) from external sources to not only provide visibility to such events but also use AI/ML to predict arrival times, likelihood of delays and the potential impact of such events on inventory, service levels and customer experience. Armed with such powerful insights, companies can collaborate with their supply chain partners using Situation Rooms and determine corrective actions they can execute through their network to minimize the impact.
Luminate Control Tower is currently providing visibility to customers across industries and for one customer, a global medical technology company, it is putting into sharp focus the crisis at the Port of Los Angeles, Port of Long Beach and Port of New York where over 100 containers across 50 vessels are being tracked.
To learn more watch LCT in action.