Recently a team from Blue Yonder attended the Forum Automotive Logistics 2025 (FAL25) industry conference in Dresden, Saxony, Germany.
True to the theme of the conference — “The New Age of Exploration — All Hands on Deck!” — the focus was on innovations and discoveries that are enabling the world’s automakers to achieve new levels of supply chain excellence. Hundreds of decision-makers and experts came together at FAL25, which was sponsored by the Association of the Automotive Industry (VDA) and the Federal Association of Logistics (BVL).
Kai Althoff, CEO of BVL, said, “No other industry is undergoing a similar transformation like the automotive sector. Geopolitical shifts, the question of semiconductor supply, difficult location and infrastructure conditions, and poorly predictable sales development are additional challenges for the industry. Logistics is the link for everything and must successfully accompany the changes.”
While the automotive industry’s current challenges were highlighted, there was a palpable sense of energy and optimism at FAL25 — because the solutions are readily available to address these challenges. The focus at FAL25 was clearly on the development and relevance of new digital technologies. I was fortunate to speak at the conference, joining other speakers that included both Blue Yonder customers and other global automotive industry leaders — including Mercedes-Benz, Porsche, Volkswagen and AUDI.
In my presentation, I didn’t minimize the significant challenges faced by automakers, from demand uncertainty to parts shortages. But I did bring a sense of optimism, because Blue Yonder has worked hard to understand and address these challenges, positioning original equipment manufacturers (OEMs) and their suppliers for a bright future. Discovery and exploration were fitting themes as I invited attendees to learn more about Blue Yonder’s innovative solutions for the auto industry.
Digital transformation is no longer optional
Called “Supply Chain Management Reinvented,” my presentation at FAL25 demonstrated the power of end-to-end digitalization and solution interoperability to truly transform automotive supply chains.
Despite the complex demand and supply forces they’re facing — forces that impact the entire supply chain network — most companies in the industry are not taking a holistic approach to supply chain optimization. They’re still embracing point solutions to address specific activities like demand forecasting or production planning. That’s certainly led to some gains in inventory accuracy, assembly line utilization and other functional metrics.
But disconnected point solutions, acting separately, simply can’t keep up with the rapid pace of change today, or consider the interconnected nature of the modern supply chain. For example, by the time the procurement team recognizes a chip shortage, the sales team might have taken hundreds of new orders that require the missing chips — and many vehicles that also need chips may already be in production.
Similarly, a sudden regional demand spike might lead automakers to quickly and eagerly slot a certain car model into production in large quantities — only to find that a driver shortage or a port closure means those vehicles can’t be immediately delivered.
We all know the consequences of these cases of supply chain misalignment: Excess, aging inventory on the one hand, and lost sales and idle production lines on the other hand.
In a traditional automotive supply chain, companies have created various connections across their internal organizations, as well as with trading partners. Those connections come in all types. Some are sophisticated and hard-coded, while others are based on informal email exchanges and manual file-sharing. Here are some problems with that traditional, nondigital approach:
- Because connections are point-to-point, and set up manually, connections are easily broken whenever any partner updates their functional or corporate system.
- Data is fragmented between trading partners, and even within the automaker’s organization, which means partners are guided by multiple versions of the truth.
- There are whole sets of information that would better inform decisions both upstream and downstream — but blind spots exist instead, because nobody can access the right information, let alone in real time.
- Because of these blind spots, decisions become siloed. Every function, and every trading partner, focuses on their own narrow metrics that may not be aligned with the success of the larger supply chain.
The power of the network effect
At Blue Yonder, we recognize that the true power of digitalization lies in using advanced software to tie the end-to-end supply network together in real time, fed by the same data and aligned with the same goals. Sure, an advanced production scheduling (APS) solution is powerful, and so is a transportation management system (TMS). But their power is exponentially amplified when they’re tied together on a foundation like Blue Yonder Platform in real time.
Connected on Blue Yonder Platform, cloud-native software solutions share the same data and work together in an orchestrated manner, supported by interoperability. As soon as supply planners recognize a parts shortage or inbound delivery disruption, that event is communicated across all functions in real-time. Sales team members can alert customers. Production can be dynamically replanned. Labor, outbound delivery ships and trucks, and other resources can be re-assigned.
How is this end-to-end, dynamic orchestration possible? Because the entire supply chain shares the same data, and the same predefined performance targets, artificial intelligence (AI) and machine learning (ML) can take over the data ingestion and analysis — and even pull resolution levers across functions to bring the supply network back into alignment.
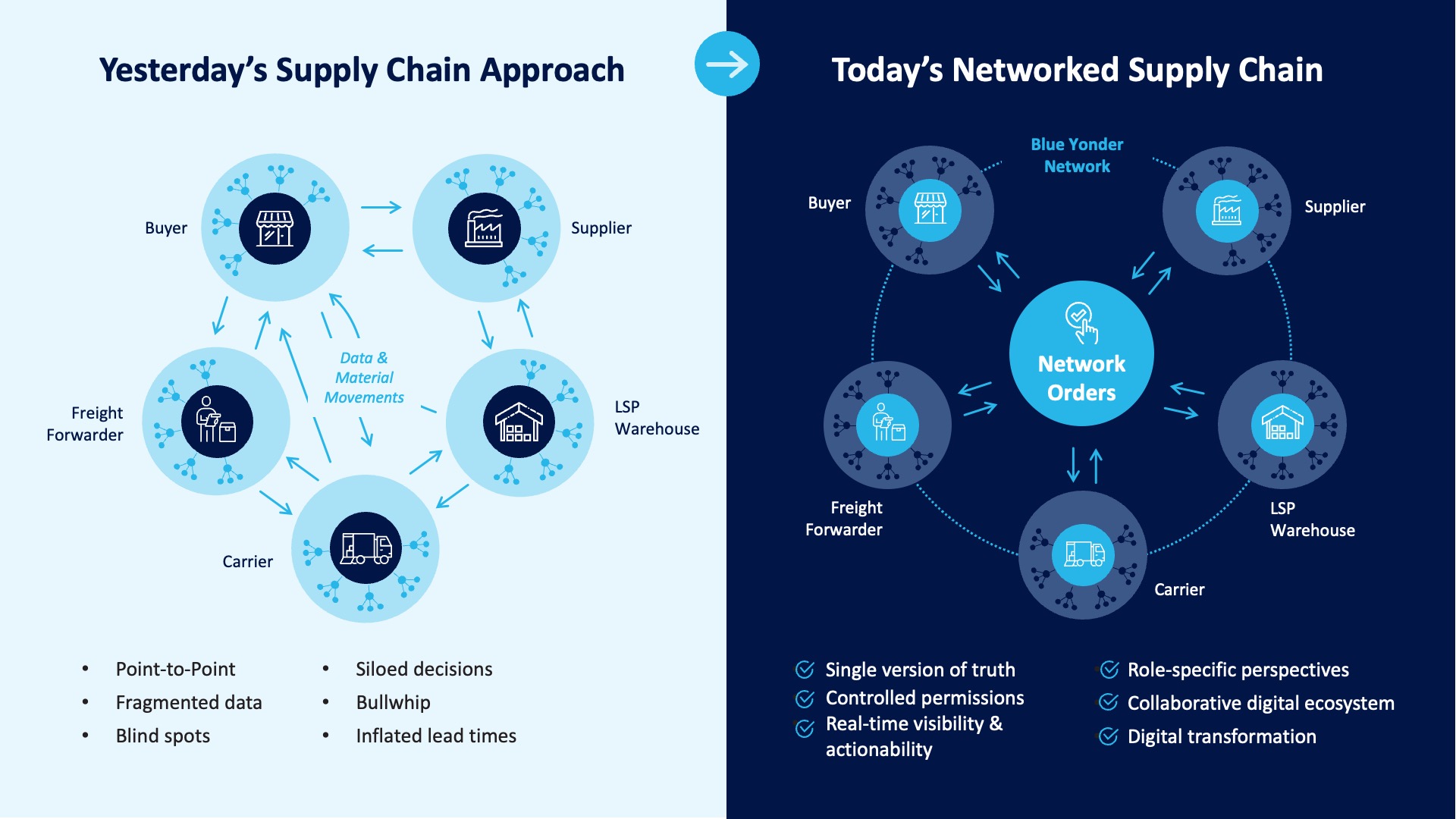
While human cognition and manual analysis are simply incapable of considering the end-to-end impact of an isolated event, for AI it’s easy. AI-enabled decision engines ingest upstream and downstream data, apply predictive analysis and course-correct the supply chain, usually in mere seconds.
As a result, the outcomes of disruptions become more profitable and — thanks to what-if scenario planning enabled by AI and ML — more predictable. Even amid volatility and uncertainty, automakers can be more confident that their cost and service results will stay on track toward predefined performance targets.
Blue Yonder calls this the network effect, and it’s an absolutely critical mindset for every OEM and supplier today. After all, when a disruption or execution occurs in one node of the supply chain, it affects every other node, network-wide. Without real-time connection and collaboration, disconnected point solutions and disparate manual planning processes might actually be working at cross purposes, with disastrous impacts on overall cost and service metrics.
Blue Yonder’s holistic approach, combined with our industry-leading solutions that span the supply chain, help automotive customers manage uncertainty and remain resilient. The integration of connected demand planning, supply planning, production planning and logistics planning data ensures decision-making is based on complete visibility. Every network stakeholder knows what’s happening, what’s needed and what’s possible in real time, all the time.
Discover the value of Blue Yonder
While the challenges discussed at FAL25 are formidable, the Blue Yonder team left the event feeling energized and inspired about the future of automotive supply chains. We saw a community focused on exploring the real-world value of digitalization to transform this industry in the face of its unprecedented challenges.
At Blue Yonder, we’re big believers in the power of advanced technology for one simple reason: We’ve seen firsthand the value it’s delivered to dozens of automotive customers. While the industry’s complexity and challenges have increased, we’ve invested in innovations like AI, Platform and interoperability to equip our customers for future success, no matter what tomorrow brings.
Want to explore the potential of Blue Yonder — and get all hands on deck for supply chain transformation? Contact us today, and let’s embark on a process of value discovery together.