Supply chains for medical devices are getting increasingly complex and face unique challenges. Many of the most complex medical device supply chains exist within large conglomerates producing a myriad of diverse products from pacemakers to testing kits and from MRI machines to disposable needles. The sheer diversity of the products that need to be managed warrants a robust and scalable planning solution.
Some of the challenges faced by today’s medical devices manufacturers are:
Diversity of Products: Large medical device manufacturers often have a diverse portfolio and hence very different supply chain structures for each of them. Some of the products like testing kits, disposable needles and other fast-moving items need a Make to Stock (MTS) supply chain while others like MRI machines and CAT scanners need an Assemble To Order (ATO) supply chain planning solution. This creates a need to segment the supply chain and have separate inventory norms for each of the product lines. Also due to the diverse regions that the manufacturer supports, the inventory strategies need to be different to cater to the different markets.
Solution: Blue Yonder Inventory Optimization solutions offers the right segmentation strategies to cluster the demand across multiple dimensions of product, location and customer. The dynamic segmentation and inventory optimization strategies offered integrated seamlessly with the demand planning systems to accurately provide safety stock norms based on the diverse service levels across different customer markets.
New Product Introduction: Medical devices face a unique challenge as compared to other segments in the area of New Product Introduction. The reason is that the rules and regulations for these products are different depending on the market. The time required to certify the new products are market dependent. Hence a new product could be active faster in the U.S. than in European countries due to more stringent guidelines. It also depends on who controls the health services in the country. Countries like U.S. are primarily driven by private players and insurance driven while in countries like France and Spain the government provides virtually free health services but imposes higher taxation. The approval times between such diverse countries are very different and the new products or the Phase In products need to be introduced at different times in different markets. This provides a unique challenge in the supply chain to maintain country-specific stocks and date effectivity for the transition.
Solution: Blue Yonder Supply Chain Planning solutions offers a robust Phase In / Out solution not only from a demand planning perspective but also from a supply planning perspective. The solution offers a mechanism to not only plan for the demand for new products by market but also helps to define the alternate relationships between Phase In and Phase Out products by market with date effectivity. This way we can define the Phase In and Phase Out relationship such that based on the demand or safety stock requirement from the market, we could consume the Phase Out product first before producing fresh on the Phase In product. In some cases, we could even define that the Phase In product is not applicable before a certain date and hence the production will not be triggered for the new product for the market’s demand where the new product is not yet approved. These options in the configuration allow to reduce the stock and blocked working capital at the same time adhering to the country-specific regulations.
Compliance and Regulatory Needs: Most of these organizations have a single source for each of their products but serving almost the demands for the entire world. The regulatory requirements in each of the countries is different and unique to that country. Also, they keep changing as time passes by and new regulations are created. These regulations warrant that the product be manufactured using certified manufacturing processes. While some countries provide relaxed norms some other countries have more stringent norms. The company would lose opportunity to manufacture at lower costs if all the products are manufactured with the most stringent of norms. At the same time, it would end up with obsolete stocks and maybe lawsuits if the product is manufactured using less stringent norms and it makes their way to the more stringent countries. These intricacies result in SKU proliferation, therefore making stock management and production planning becomes a major challenge and requires a delicate balance between margins and adherence to norms.
Solution: Blue Yonder Supply Chain Planning solutions offers attribute-based planning capability to respond to regulatory requirements specific to a given country. This allows for flexibility to choose the production process to use or a particular raw material stock to use during the manufacturing process based on which markets’ demand or safety stock is being satisfied. It provides an end-to-end visibility right from raw material consumption to finished product manufacturing to shipping across the multi-echelon network to the final destination. This guarantees that based on the market, the lowest cost eligible manufacturing process would be given higher preference than a higher cost one. Hence it minimizes the cost of manufacturing while adhering to the most stringent norms.
Perishable Products: One might assume that since many medical devices share similarities with electronics products, their shelf life is considerably larger than the pharmaceuticals or food and beverages. While this is true, it is also true that medical device manufacturing customers often have stringent shelf life requirements. Hence, it’s not uncommon to see that a product that has five years of total shelf life has a demand placed on it with a condition that at the point of sale, the minimum shelf life is four years. This means that any product that is manufactured one year back cannot be sold. To complicate matters, many of these products have a large economic order quantity due to setup times in changeovers. This can lead to excess manufacturing and write-offs. Again, similar to the regulatory norms, not all the customers / markets have these high minimum shelf life requirements. Therefore, some of these products can be shipped out to destinations with lower minimum shelf life requirements. This would be desirable to reduce the overall production and clean-up of excess stocks.
Solution: Blue Yonder Supply Chain Planning solutions offer ways to manage perishability using customer- / order-driven minimum shelf life requirements. Hence the excess stock available on slow movers can be easily cleaned up by demand from markets that require lower minimum shelf life requirements. This minimizes the overall stocks held by the organization and hence unblocks the working capital.
Diverse Shipping Lead Times: Because a given product is often manufactured in one country and shipped to locations across the world, the distance and hence the lead time of shipment from the manufacturing locations to the demand location is often very different. This offers a unique challenge in terms of prioritization of demand. Typically, the demands from the markets are prioritized based on the due date at the customer location. If this was applied to this type of supply chain, then the constrained capacity would be allocated first to the nearest market while the farther markets would be starved. There is a need to provide a fair share of the capacity to all markets and hence a need to prioritize the demand differently.
Solution: The prioritization in this case should be done based on the estimated manufacturing date at the plant based on the lead time offsets rather than the due date of the demand as done at most customers. The fair share layers also can be defined based on this prioritization scheme to give near equal priority between the nearer and farther markets with respect to the manufacturing locations.
Reverse Supply Chain: One unique challenge in this industry is the presence of what is called return stocks. Many of the products are required during complex surgical procedures and these products may or may not be used during the surgery. So many of the hospitals (customers) would order all variants of the product or even multiple products as a kit. These being expensive products they would have a contract that only the products that are consumed be billed while the rest would be returned. When the products are used during a surgery, they can still be returned to the manufacturer but require an extensive sterilization process. This creates a reverse supply chain problem where the stocks that are projected to be returned cannot be again used to satisfy the same demand causing a cyclicity in demand-supply.
Solution: Blue Yonder Supply Chain Planning solutions incorporate a robust attribute-based planning algorithm with which the projected return stocks can be tagged in such a way that it can be used to satisfy only demands other than the ones from which the supply would be returned from. This makes sure that cyclicity between the supply and demand is broken and at the same time, these stocks can be utilized to meet other demands.
Conclusion:
Organizations supplying medical devices have unique challenges like single sourcing with country specific requirements, diverse product portfolio and perishability. Blue Yonder solutions provide an integrated supply chain planning suite to address all these constraints to generate make, move and buy plans allowing to minimize the overall stock at a higher demand satisfaction.
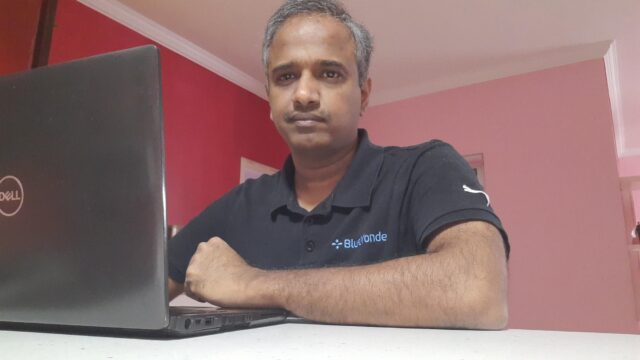
This blog post was written by Shyam Chittal, a Senior Distinguished Functional Architect with Blue Yonder’s Cognitive Business Planning team.