5 Years Later: 3 Things COVID-19 Changed in Supply Chain And 2 It Didn’t
March 11th – a date that marks five years since the World Health Organization (WHO) declared the COVID-19 a pandemic. A wave of chaos followed that turned the supply chain upside down, forcing it to adapt, transform, and learn at an accelerated pace.
As well as adapting to a global pandemic, the supply chain has faced a seemingly relentless barrage of ‘unprecedented times’: The Suez Canal blockage, devastating wildfires, the war in Ukraine, escalating Red Sea tensions, persistent chip shortages, crippling labor shortages, and the looming specter of new tariffs… The list goes on.
As we mark this somber anniversary, we look back on the three most significant, long-lasting impacts that have fundamentally reshaped supply chain operations, and, perhaps more surprisingly, the two areas that have returned to a semblance of normalcy.
3 long term changes to the supply chain
1. A rise in nearshoring and away from single-source dependency
The pandemic was a wake-up call that exposed the fragility of globally interconnected supply chains and the risks of over-reliance on distant suppliers and single-source strategies. Although globalized supply chains are efficient in stable times, they are highly vulnerable to sudden, widespread shocks – which was seen during the initial lockdowns and border closures.
The pandemic showed vulnerabilities in the supply chain, which were amplified by subsequent events—such as the Red Sea tensions, which caused cargo traffic to fall from around 5000 containers per day in November to 2000 in December 2023. Or the Panama Canal drought, which forced authorities to cancel ship crossings by 36%, costing between $500 million and $700 million.
The result was a shift and acceleration towards nearshoring, reshoring, and source diversification. Nearly 8 out of 10 companies (79%) are now diversifying their supplier base, with 71% actively investing in regionalization and localization to mitigate future disruptions.
McKinsey research shows that 73% of companies are now pursuing dual-sourcing, and 60% are regionalizing their supply chains. This shift reflects a direct response to the pandemic’s disruption, which exposed the dangers of relying on a single point of failure.
In addition, there is also a rise of “friend-shoring,” with 83% of organizations investing in it, which demonstrates a desire to build more stable and predictable supply networks. The pandemic highlighted the importance of geopolitical stability and trust, driving companies to prioritize partnerships with political and economic allies.
The pandemic acted as a powerful catalyst, accelerating the adoption of regionalization, diversification, and resilience-building strategies. It forced companies to re-evaluate their supply chain models, moving away from purely cost-driven approaches to embrace a more robust and adaptable framework.
2. Rapid development of advanced planning and scheduling tools
The COVID-19 pandemic didn’t just expose the vulnerabilities of physical supply chains; it also revealed the critical need for digital agility. The sheer volume of “unprecedented” events over the past five years has underscored the absolute necessity for real-time information and proactive risk management, particularly within Advanced Planning and Scheduling (APS) systems.
Before the pandemic, many companies relied on static, reactive planning methods. The sudden and unpredictable nature of the pandemic revealed a need for a more dynamic and responsive approach, that can quickly adapt to shifting demand, supply shortages, and logistical bottlenecks. This urgency fueled a significant investment in APS systems, which offer the ability to simulate various scenarios, predict potential disruptions, and optimize resource allocation in real-time.
A McKinsey survey highlights a strong demand for AI-based tools, particularly in demand planning, where 74% of respondents show keen interest. Elsewhere, two-thirds of survey respondents report making substantial progress in implementing APS systems, showing that these tools are no longer a luxury, but a critical component of modern supply chain digitization.
3. Labor strategies have become critical
The past five years have been marked by persistent and varied labor shortages. Initial lockdowns caused widespread operational disruptions, bringing many sectors to a virtual halt. Even as lockdown restrictions have loosened, shifts in nearshoring, remote work, and the increased complexity of supply chain planning, have caused increased labor shortages across all areas of the supply chain.
Descartes research shows that 76% of supply chain and logistics leaders are experiencing notable workforce shortages, with a concerning 37% characterizing the resource shortage as “high to extreme”. The areas most affected by labor shortages were transportation operations with 61% of businesses affected, followed by warehouse operations at 51%, as well as transportation planning and inventory/distribution at 51%.
Ongoing labor shortages and demands continue to reshape supply chain dynamics, forcing companies to shift labor approaches from a mere cost factor to a critical component of resilience, sustainability, and competitive advantage.
The impact of labor shortages has manifested in several key ways:
- Accelerated Automation and Technology Adoption: Facing workforce gaps, companies are increasingly turning to automation and technology to ease repetitive manual tasks and improve the efficiency of their existing workforce.
- Emphasis on Workforce Resilience: Companies are now developing strategies to build a more resilient, flexible and adaptable workforce, including cross-training and contingency planning to mitigate the impact of future disruptions.
- Intensified Talent Acquisition and Training: With persistent labor shortages, particularly in skilled roles, companies are investing heavily in talent acquisition and training. This involves offering competitive wages, benefits, and opportunities for professional development to attract and retain qualified workers.
- Rising Labor Costs: Labor shortages, coupled with inflation and heightened competition for skilled workers, have led to a significant increase in salaries.
2 trends that have ‘returned to normal’
1. The e-commerce explosion didn’t replace omnichannel buying
As countries went into lockdown, e-commerce sales exploded, and consumer behavior was radically changed. At first, there was a surge in essential purchases as people stockpiled necessities like toilet paper. This quickly expanded to include big-ticket items such as furniture and technology, as the transition to remote work took hold.
This sudden and unprecedented surge in online demand led to significant supply chain strains, contributing to shortages – including the global semiconductor shortage and increased technology demand.
The below graph from the Office for National Statistics (ONS) helps illustrate this dramatic shift. From 2007 to 2019, internet sales as a percentage of total retail sales followed a steady, predictable upward trend. However, the pandemic’s onset caused a sharp spike, which has since stabilized and settled into a more sustainable growth pattern.
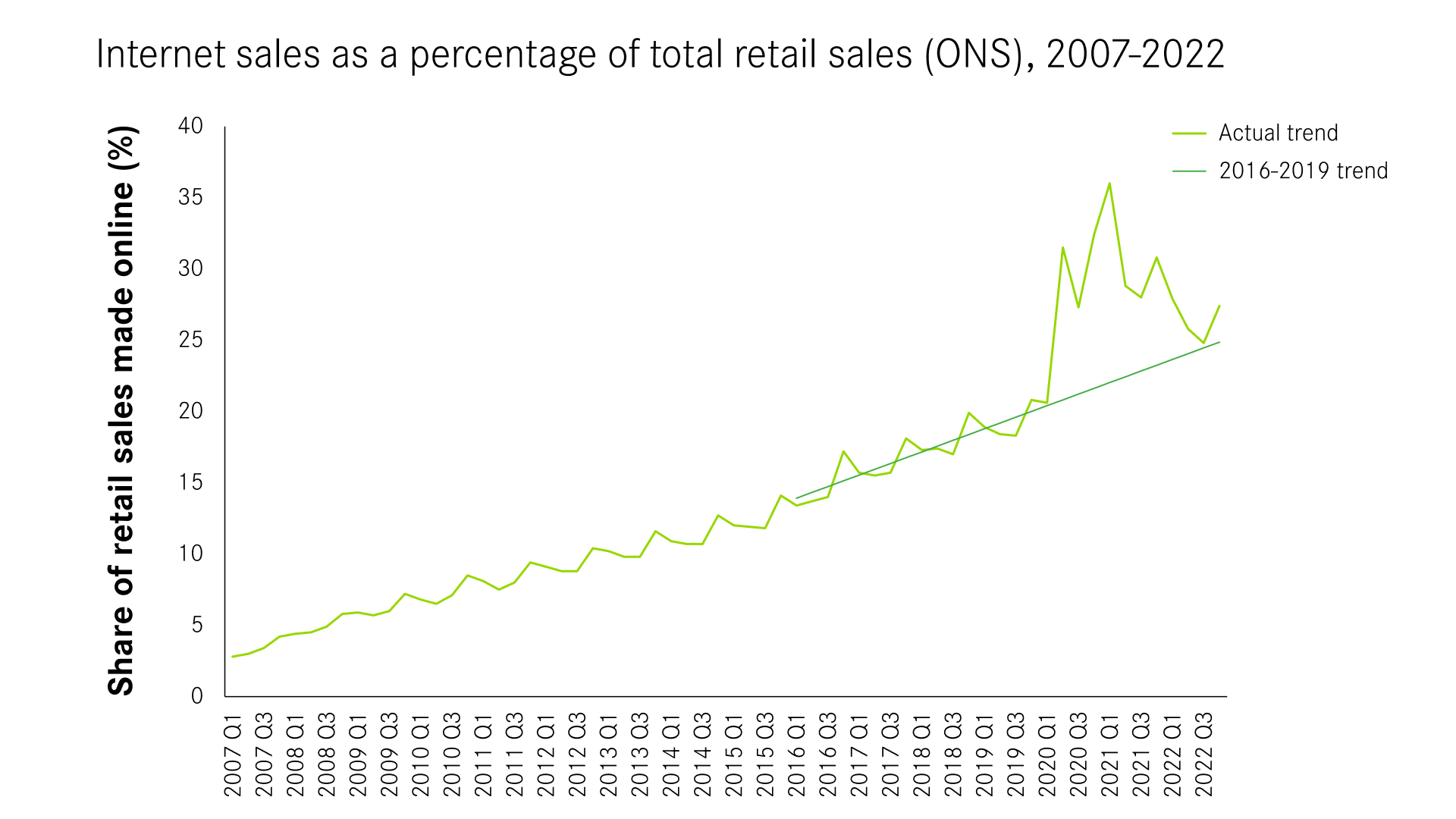
Global data also shows that in 2020, e-commerce sales represented 26.8% of global retail sales. By 2023, this had settled back down to 19.4%, putting it back on a steady upward trend to its projected 25.2% share of global sales by 2030.
The pandemic may have accelerated e-commerce, but it didn’t erase the need for a robust omnichannel strategy. Customers still demand a seamless experience, whether they’re browsing online or visiting a physical store. They’re not choosing one or the other—they’re embracing both, just as they did before.
2. The supply chain is no longer overstocking “just-in-case” inventory
To cope with the disruptions that were unleashed at the start of the COVID-19 pandemic, many businesses began stockpiling inventory to combat the fear of crippling shortages. Not surprisingly, the ‘just-in-case’ approach to keep overflowing warehouses full of stock was unsustainable in the long run.
Since the pandemic, the number of companies relying on bigger inventory buffers to manage disruptions has fallen from 59% to 34%. In addition, 46% of survey respondents intend to reduce or eliminate risk buffers, potentially returning to or even falling below pre-pandemic levels.
While some of this reduction may be due to the financial and logistical burden of buying and storing this inventory – it reflects a conscious decision to move away from excessive stockpiling and focus on a more balanced approach that prioritizes resilience without resorting to keeping excessive inventory.
How Blue Yonder has helped businesses adapt and thrive during the pandemic and beyond
The global pandemic forced companies to adapt and transform, fast. Blue Yonder has been at the forefront of this evolution, providing innovative solutions that have enabled companies not only to survive but thrive amidst disruption and change. These include:
- Advanced planning and scheduling: Blue Yonder’s advanced planning and scheduling tools have empowered businesses to move away from static, reactive methods. By leveraging data and advanced insights, these tools allow companies to predict demand accurately, simulate various scenarios, and optimize resource allocation in real-time. This capability has been crucial in navigating supply shortages and logistical bottlenecks, ensuring businesses remain agile and resilient.
- Resourcing & labor management: Blue Yonder has supported businesses in attracting, engaging, and retaining talent through comprehensive resourcing and labor management solutions. For our clients, we’ve achieved a 35% reduction in labor expenses, a 50% reduction in turnover rate, and a 25% increase in employee engagement.
- Real-time data & visibility for omni-channel excellence: The Blue Yonder Inventory Optimization provides real-time data and visibility across the entire supply chain, enabling businesses to achieve omnichannel excellence by meeting customer demands across e-commerce and in-store channels. We’ve helped our clients reach a 300% return on investment by minimizing stockouts and excess inventory, helping maintain a competitive edge in a rapidly evolving market.
Want to find out more about how Blue Yonder has helped business adapt, thrive and build resilient supply chains? Get in touch today.