Bridging Disruption: Blue Yonder Helps Customers Navigate the Tragedy in Baltimore
Who can forget watching the shocking footage of the Francis Scott Key Bridge collapse in Baltimore? When a 948-foot-long cargo ship called Dali crashed into the bridge in the early morning hours of March 26, the costs were high. Most significantly, the accident claimed the lives of six construction workers who were fixing potholes on the bridge.
The total collapse of the bridge, which happened in less than 30 seconds, also resulted in the multi-year closure of a major traffic route used by more than 12.4 million vehicles in 2023. It closed the Port of Baltimore to ship traffic. One of the Top 20 ports in the U.S., Baltimore ranks first in the movement of automobiles and light trucks. The port received 570,000 imported vehicles in 2023 alone.
In addition, cargo ships bound for Baltimore were suddenly brought to a standstill, unsure how to proceed. And, as this blog is published, the Dali remains in the Port of Baltimore, loaded with cargo containers and trapped by bridge debris. It wasn’t until this week that the first container ship was able to enter the port; however, ships will be limited due to the channel depth and width that was opened.
Shippers Pivot Strategically, in Near Real Time
While it’s impossible to anticipate this kind of disruption, Blue Yonder customers leveraging our control tower solution had a critical advantage. They were already using advanced Visibility, Collaboration and Network microservices, hosted on the Blue Yonder Platform, to achieve near real-time awareness and rapid re-planning.
Immediately following the bridge collapse, Blue Yonder’s control tower support team used advanced search engines to quickly identify any customer shipments that were stranded on the Dali cargo vessel. Of 56 shipments passing through the Port of Baltimore at the time of the accident, the team identified four affected shipments that were aboard the Dali. Blue Yonder reached out to those customers to help facilitate an optimal solution.
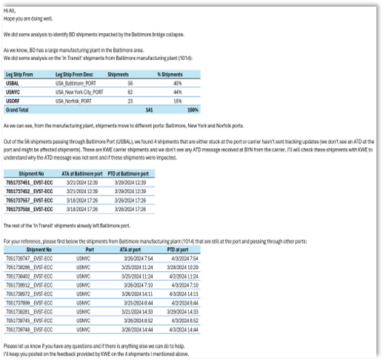
Beginning right after the accident, and continuing today, control tower capabilities from Blue Yonder are helping many other customers strategically re-route their shipments, using alternative ports from New York to Georgia. The dashboard map and shipment detail screens have proven especially invaluable in enabling customers to model new routes, see the cost and service impacts of those options, and make quick decisions to keep their products moving.
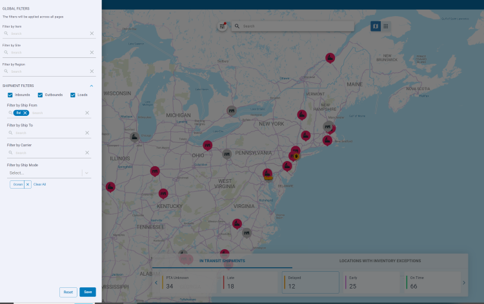
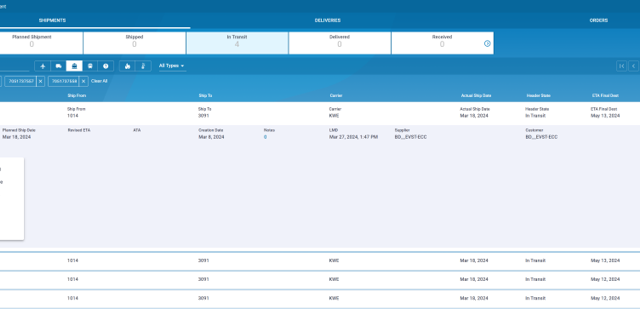
Blue Yonder Adds New Capabilities, Also in Near Real Time
But customers weren’t the only ones pivoting quickly. Blue Yonder’s core control tower team quickly seized an opportunity to provide even greater assistance. They enhanced the “chokepoint report” capability in the control tower solution to add the Port of Baltimore as a major chokepoint, or routing obstacle.
This new feature makes it much easier for customers to filter their shipments — by current geographic location, origin site, destination site, and proximity to Baltimore — and flag those affected by the port closure. The new chokepoint report will help planning teams continue to target shipments that need to be rerouted.
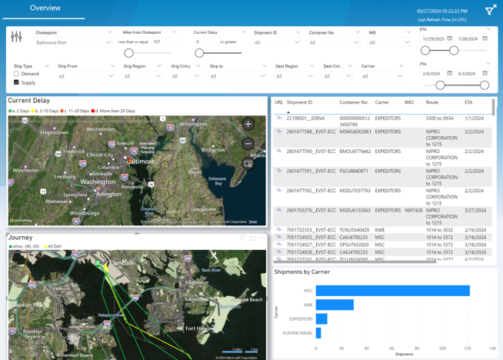
Increase Your Resilience, No Matter the Disruption
There’s no telling when operations will normalize at thePort of Baltimore, or when the next disruption of this magnitude will occur. One thing is certain: Those companies using advanced control tower capabilities will always be far better prepared for the unexpected.
Control tower capabilities from Blue Yonder — delivered as Visibility, Collaboration and Network microservices — are purpose-built to deliver near real-time transparency and awareness across the end-to-end supply chain. They can be deployed as plug-ins across all of Blue Yonder’s flagship planning and execution software.
The result? Working together, these solutions can ingest both internal and external data, then leverage advanced artificial intelligence (AI), machine learning (ML), data science and predictive analytics to assess the impact of upcoming events — and execute strategic interventions. By installing end-to-end control tower functionality, companies can drive a synchronized, orchestrated response that minimizes negative impacts, maintains high service levels and protects profit margins.
Running natively on the Blue Yonder Platform, control tower microservices can be deployed quickly and cost-effectively, often in days or weeks, instead of months. Companies can accelerate their time to value, while preparing in advance for the next big supply chain disruption.
Contact us to learn more about how Blue Yonder can support your own disaster preparedness plan.